Made in China, Lost in Combat: The U.S. War Machine’s Fatal Flaw
America’s War Chest Is Running on Fumes—and Silicon Valley’s Defense Elite Is Sounding the Alarm
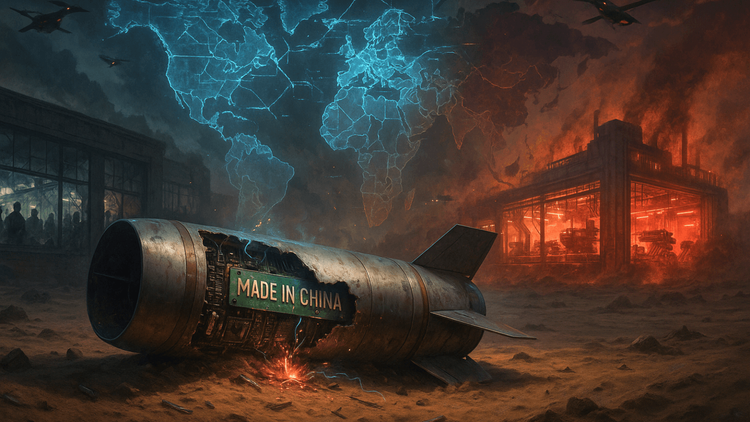
The United States, often seen as the undisputed heavyweight of global military dominance, is running dangerously low on the very thing it needs to fight wars: munitions. Trae Stephens, co-founder of defense tech startup Anduril and partner at Peter Thiel’s Founders Fund, just delivered a chilling dose of reality. Speaking on Auren Hoffman’s “World of DaaS” podcast, Stephens made it brutally clear—if America were dragged into a hot war with a near-peer superpower, its stockpile of missiles and bombs would be gone in a week.
This isn’t speculation. This is an alarm bell from one of the most connected minds in defense innovation. And it should terrify anyone who’s been lulled into thinking the U.S. military-industrial complex is untouchable.
Stephens didn’t sugarcoat it. He pointed out that the U.S. military’s procurement strategy has become a web of overly customized, overly expensive, and supply-chain-fragile systems. While these advanced weapons may be impressive on paper, they’re manufactured in small batches and are excruciatingly slow to replenish. Translation: they look great at defense expos, but they don’t hold up when the missiles are flying fast and the pressure is real.
One particularly damning example is the ongoing conflict in the Middle East. Saudi Arabia, a critical U.S. ally, is taking consistent fire from Houthi rebels. And yet, the U.S.—purportedly the world's defense supplier of last resort—can’t get enough Patriot missiles into Saudi hands. As Stephens laid out, Riyadh is now forced to shop around to other countries just to keep its air defense systems online. That’s not just embarrassing. It’s strategic negligence.
Then there’s Ukraine, where the U.S. has been flooding the battlefield with high-tech military aid. But the cost of that support is becoming clear back home. According to Stephens, the Pentagon isn’t just giving away surplus—it’s drawing from active U.S. reserves. That means if a crisis erupted tomorrow in Taiwan or the South China Sea, America might have more press releases than precision-guided munitions.
Things have gotten so dire that defense contractors are reportedly begging retired workers to come back and man the old assembly lines. Picture that. The world’s most advanced military calling grandpa out of retirement to crank out 1970s-era missile systems. It's not just unsustainable—it’s absurd.
And this crisis didn’t come out of nowhere. Stephens’ partner in Anduril, Palmer Luckey, offered his own blunt diagnosis in a separate interview with music producer Rick Rubin on the Tetragrammaton podcast. According to Luckey, America’s manufacturing hollowed out over decades because it was more profitable to ship factories to China. That short-term gain—cheap TVs, cheaper labor, and lax regulations—has now turned into a long-term strategic liability.
Luckey, the controversial wunderkind behind the Oculus Rift and now the CEO of Anduril, didn’t hold back. He laid the blame squarely on U.S. policymakers who welcomed China into the World Trade Organization without building guardrails. The consequence? America outsourced its industrial base to a country that now sits across the table as a geopolitical rival—and maybe a future adversary.
According to Luckey, the U.S. got fat and comfortable. The cheap goods flowed in, and the hard questions were ignored. Who would make the microchips? Who would manufacture the missiles? The assumption was that global supply chains would never break. But COVID-19, the war in Ukraine, and the looming Taiwan flashpoint have shattered that fantasy.
Adm. Samuel Paparo, head of U.S. Indo-Pacific Command, confirmed these concerns in a speech to the Brookings Institution late last year. He admitted that sending arms to Ukraine and Israel is “eating into stocks.” That’s not political spin. That’s a military commander saying that if China invades Taiwan tomorrow, the U.S. might not have the arsenal to respond with strength.
It’s hard to overstate how damning that is. America is not only the world’s largest military spender—it’s the country everyone else expects to come to the rescue. And yet, behind the Pentagon’s trillion-dollar budget lies a brittle production ecosystem, where sophisticated weapons are built in boutique factories, on timelines that stretch for years, not days.
Stephens’ warning should be a wake-up call for policymakers, defense contractors, and voters alike. The United States can no longer rely on a peacetime procurement model in a wartime world. The age of just-in-time inventory and slow, customized military tech is over. If America doesn’t reindustrialize with urgency, it risks being outgunned in a future where speed, scale, and resilience determine victory.
Both Stephens and Luckey are calling for more than just investment—they’re calling for a cultural shift. One that values domestic manufacturing, rewards redundancy over elegance, and prioritizes readiness over margin. They’re not saying America should retreat into protectionism. They’re saying America needs to relearn how to build—at scale, and under pressure.
And they’re not wrong.
The clock is ticking. The global chessboard is shifting. China is watching. Russia is rearming. Iran is testing. America can either become the arsenal of democracy again—or it can continue ordering munitions like it’s shopping for luxury cars. But if the latter path continues, the next war won’t be won in a week. It’ll be lost in one.
Conclusion
America’s military edge isn’t guaranteed—it’s built on factories, supply chains, and the ability to surge production when the world erupts. What Stephens and Luckey are warning us about isn’t theoretical. It’s operational. The world is already burning in multiple places. And if we don’t act, the next fire might be one we can’t put out. The United States has the talent, the capital, and the history to build its way out of this hole. The only question is whether it has the will.
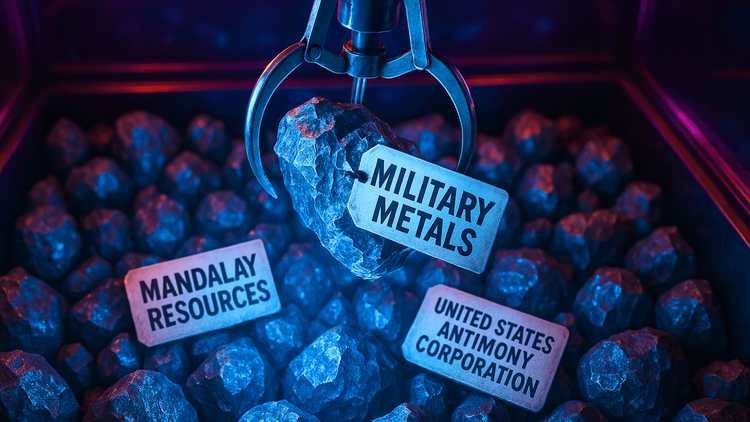