Artillery Shells in Demand: How the Army is Racing to Ramp Up Production
How the U.S. Army is accelerating efforts to eliminate bottlenecks in artillery shell production to meet global demand.

The U.S. Army is facing one of its greatest logistical challenges in recent history—scaling up artillery shell production to meet the demands of current and potential global conflicts. A major bottleneck in the production of 155mm artillery shells has been identified, with the service relying on a single source that is struggling to keep up with the pace. However, significant efforts are underway to diversify suppliers, streamline processes, and increase output, ensuring the Army is better prepared for future challenges.
This article will explore the ongoing efforts by the U.S. Army to ramp up production of 155mm artillery shells, the challenges they face, and how the current global geopolitical landscape is pushing the U.S. military to act swiftly.
Why 155mm Artillery Shells Are Crucial for Modern Warfare
Artillery has long been referred to as the “king of battle” due to its overwhelming impact on the battlefield. The 155mm artillery shell is a key component in modern warfare, delivering powerful firepower at long distances, providing ground forces with a critical advantage in both offensive and defensive operations.
The ongoing war in Ukraine has sharply illustrated the importance of these munitions. Ukrainian forces have been burning through artillery shells at a rapid pace, using them to hold off Russian advances and to launch counteroffensives. This heavy reliance on artillery has placed immense pressure on U.S. and allied stockpiles, highlighting the need for a more robust and flexible production system.
The Bottleneck in Production
Before the war in Ukraine, the U.S. could only produce about 14,400 artillery shells per month, a number that is woefully inadequate for the demands of modern warfare. The Army has traditionally relied on a single source for its 155mm shell production, which created a significant vulnerability in the supply chain. Should anything go wrong at this facility, it could jeopardize the entire production process.
Historically, the U.S. produced its artillery shells at a single plant in Scranton, Pennsylvania, and a nearby privately operated facility. Once produced, these shells were transported to the Iowa Army Ammunition Plant, where they were filled with explosives. This setup was highly centralized, making it susceptible to delays or disruptions.
The Army's Push to Diversify and Expand Production
To overcome the bottleneck, the Army has diversified its production base. One of the major steps in this direction is the opening of a brand-new facility in Mesquite, Texas. This facility, run by General Dynamics Ordnance and Tactical Systems, is primarily automated and leverages production systems imported from Turkey. It represents a critical part of the Army’s plan to scale production and reduce reliance on any single plant.
In addition to the Texas facility, the Army has also contracted shell production to IMT Defense, a company based in Ontario, Canada, and established a new Load, Assembly, Pack (LAP) plant in Camden, Arkansas. These moves represent the Army’s strategy to spread production across multiple locations to minimize risks and ensure a more stable flow of artillery shells.
U.S. Army's 2025 Target: 100,000 Shells Per Month
Despite the expansions, the Army is still racing to meet its ambitious target of producing 100,000 artillery shells per month by 2025. Currently, production stands at around 40,000 shells per month, with plans to increase this to 55,000 by the end of 2024.
While the Army has made significant strides in boosting production, it has acknowledged falling behind schedule. However, officials remain confident that with the new facilities coming online and additional contracts being awarded, the service will eventually meet its production goals.
Global Efforts to Increase Munitions Production
The Pentagon has recognized the need for a global approach to increasing artillery shell production. In 2023 alone, the U.S. awarded $1.5 billion in contracts to companies worldwide to procure critical components such as bulk energetics, including TNT and IMX-104 explosives, as well as primers and fuses.
One of the critical components of 155mm artillery shells is the propellant that powers them. Up until recently, all propellant for U.S. munitions was produced at a single facility in Valleyfield, Canada. Recognizing the danger of such a single-point dependency, the Army is now setting up a new propellant production line at the Radford Army Ammunition Plant in Virginia, which will work alongside the Valleyfield facility to meet growing demand.
Securing the Future of Artillery Production
The U.S. currently relies entirely on imported TNT for its artillery shells, a situation the Army is eager to change. Plans are already in place to build a domestic TNT production facility, likely at the Radford Army Ammunition Plant. Once a contract is awarded, the Army expects the facility to be operational within 48 months.
The Army is also working to secure other key components of artillery shells, such as combustible cartridge cases. Currently, these cases are produced by Armtec Defense Technologies in California, but the Army is shifting production to safer locations like Texarkana, Texas, to reduce risks from natural disasters, including earthquakes.
Conclusion
The U.S. Army is in a race against time to overcome the bottlenecks in its artillery shell production. As global conflicts escalate and the demand for 155mm artillery shells surges, the Army is taking bold steps to ensure it can meet the needs of its forces both now and in the future. Through diversification of suppliers, investment in new facilities, and strategic planning, the Army is on track to drastically increase its production capacity. However, the road ahead is filled with challenges, and only time will tell if these efforts will be enough to meet the immense demand that modern warfare presents.
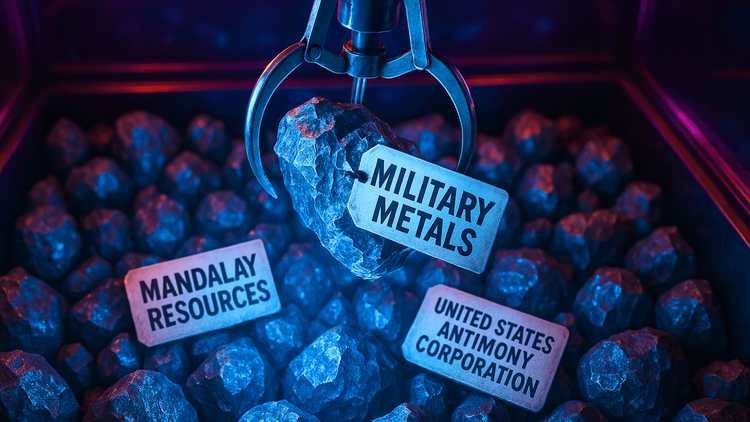